We’ve been the leader in high capacity Stereolithography & SLS for more than 20 years.
choice for:
- Form and Fit testing of new designs
- Functional parts for special projects
- Architectural models and one-offs
- Form and Fit testing of new designs
- Testing of new designs or reverse engineered parts
- Investment Casting patterns for QuickTurn cast metal parts
- Limited run production parts
Material choices include:
- SL5240 Polypropylene-like resin
- SL7520 high strength resin
- WaterShed 11120
- WaterClear 10120
- Somos Raven 7620
- SL7870 Polycarbonate-like resin
Additional SLA specs & info:
Dimensional tolerances:
- +/- 0.005” or better for the first 3 to 4 Inches
Layer thickness:
- 0.002” to 0.006 depending on resolution
Build envelope:
- 20” x 20” x 24” (up to 10’ long by special order)
Delivery:
- Depending on size of part, but typical Turnaround for hand-held parts is 24 to 48 hours.
Wax patterns Replacement:
- Quickcast Patterns are used as wax patterns for investment casting of metals such as aluminum, steel, bronze, etc. (See Metal Castings).
Finishing types:
- 2A Finishing: Minimum surface sanding and a bead blast finish. Ideal for engineering check models and form/fit testing 3A Finishing: Each part is sanded and hand-finished, benched, and verified for dimensional accuracy and surface integrity. Ideal for marketing samples, trade show samples and ready for painting. Paint and Texture: Parts are painted and textured to exact color match and specified texture. A 3A finish is required prior to paint and texture.
Stereolithography
Rapid prototyping stereolithography manufacturing gives engineers, designers, and inventors dimensionally accurate plastic parts they can hold, test, and show in a matter of days, instead of the weeks or months it used to take with conventional manufacturing.
Stereolithography (aka SLA or 3D layering or 3D printing) produces three-dimensional solid plastic objects directly from CAD data in a process that utilizes a ultra-violet laser and a large vat of photo-curable polymer liquid plastic. Working from a CAD file, stereolithography solidifies the polymer into precise patterns using a laser beam. Since they are created directly from 3D designs, SLA parts are extremely accurate, and are delivered with fast turnaround time without any compromise in accuracy or quality.
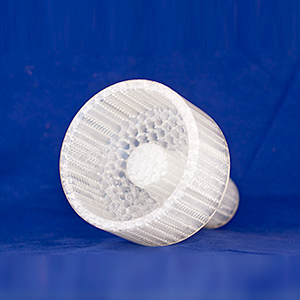
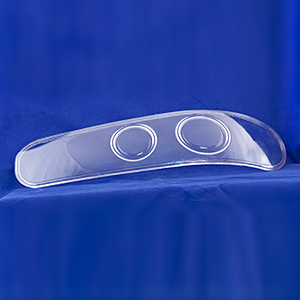
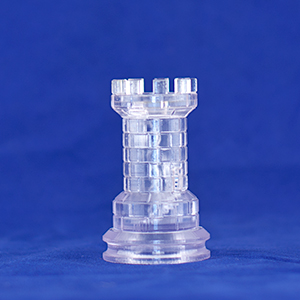
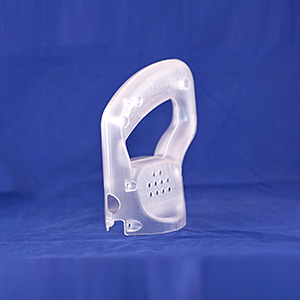
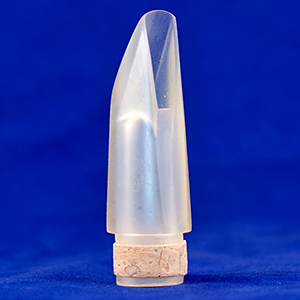
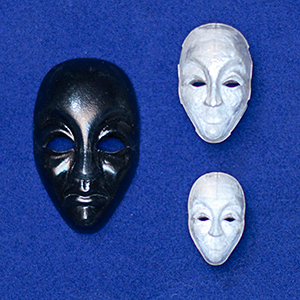
Selective Laser Sintering (SLS) is the ideal choice for:
- Prototypes that require material properties that closely replicate injection-molded parts.
Material choices include:
- Durform PA and GF
- CastForm PS
- Accura LaserForm ST-200
- LaserForm ST-100
Additional SLS Technical Data:
Dimensional tolerances:
- +/- 0.007” Depending on material
Layer thickness:
- 0.004” – 0.006”
Build envelope:
- 22” x 22” x 30”
Delivery:
- Depending on size of the part. Typical Turnaround for hand-held parts is 2 to 3 days
Wax patterns:
- Castform PS material is similar to foundry wax. SLS patterns made from this material are used in the investment casting process.
Finishing Types:
- 2A: Parts are cleaned and a bead blast applied to eliminate rough spots and remove all excess powder.
- 3A: After application of 2A finish, parts are lightly sanded and sealed with a water resistant liquid sealer creating a water proof part with smooth finish.
- 3A Paint Ready: 3A finished part is sanded and a coat of primer is applied to create a smooth finish ready for application of paint and texture.
Selective Laser Sintering (SLS)
An additive rapid prototyping process, Selective Laser Sintering (SLS) builds 3-dimensional parts from CAD data from a range of powdered materials like polyamides, nylons, or metals. Then a laser beam selectively heats and fuses (sinters) two-dimensional cross-sections or layers as an additive process. SLS provides a fast and easy way to create parts early in the design cycle, but is also suitable for limited production runs.
The SLS process is fast and parts can be nested to maximize economy, delivering a service far superior to traditional rapid prototyping or pattern cutting processes.
The SLS process allows us to build parts in both engineering type resins as well as disposable foundry waxes. The ability to produce a variety of parts quickly and accurately has given our customers a dramatic advantage in new product cycle times and overall time-to-market.
The latest generation of Selective Laser Sintering machines has given 3D-CAM an additional capability for generating patterns and prototypes.
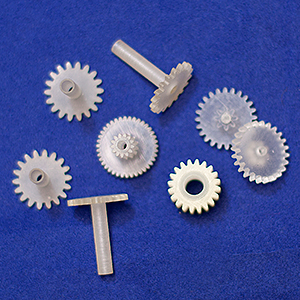
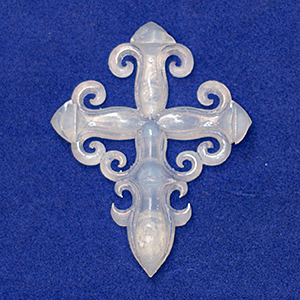
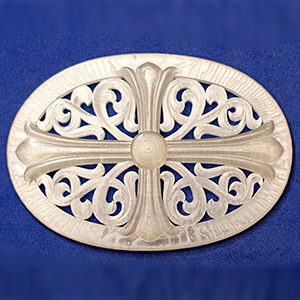
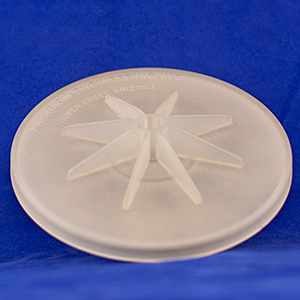